Humans have excellent vision. Compared to most animals, they can see longer distances with more colors and finer details. But the eyes that evolved to help humankind survive and thrive in caves, prairies, and jungles are no match for a world riddled with complex threats like Great Power competition, urban warfare, terrorism, and climate change. Managing those and other modern-day risks requires the ability to see more, see faster, and see better.
In the United States, the appetite for ocular advantage is fueling a remote sensing revolution that’s driven by exquisite commercial imagery from space. Emboldened by the shrinking cost and increased cadence of commercial launch capabilities, space technology companies are eager to level up their satellites with a new generation of payloads that can capture high-resolution images of Earth more often, more affordably, and with greater fidelity.
Maxar’s industry-leading WorldView Legion platform perfectly embodies those ambitions. “Launch provider competition has dropped the floor out of the cost per kilogram going to orbit,” said Keith Carrigan, a Raytheon technical fellow and technical director for the company’s WorldView Legion program. “But, to fully leverage these low-cost launch opportunities, you need to continue reducing the size, weight, and power—or SWAP—of large-aperture, high-resolution sensors so you can pair them with less costly spacecraft. That’s the second half of the overall cost reduction equation, and its exactly what our work has done.”
In 2024, four of the six planned WorldView Legion satellites were launched into low Earth orbit. The fifth and sixth satellites were launched in February 2025. Each launch carried a pair of satellites equipped with Raytheon-designed imaging instruments that provide maximal resolution with minimal SWAP—two to three times less compared to legacy sensors, to be exact. The culmination of 15 years of research and development, the instruments feature an innovative telescope design and a novel optical material that’s stronger yet lighter than previous designs. Smaller camera electronics and lighter telescopes helped Maxar reduce the mass of its entire spacecraft by a factor of greater than two, which in turn helped it reduce launch costs as well as time to orbit.
“Most companies have limited capital to expend and are looking for ways to optimize their capabilities in the market. Raytheon’s ability to provide highly capable sensors at a lower cost enables our customers to fly more satellites, that can gather more imagery, which helps companies like Maxar keep a timelier and more relevant thumb on the pulse of human events,” Carrigan said. “We’ve seen the value of that with current geopolitical conflict zones, extreme weather events, and current affairs. Maxar distributes imagery collected with our telescopes, and that imagery is shared with global media as well as government and commercial customers around the world to provide a second source of truth for what’s happening on the ground.”
“In combination with our other WorldView Legion design innovations, the sensors provided by Raytheon have helped ensure our 30 cm collection capacity advantage long into the future,” said Matt Jenkins, Maxar’s Chief Space Systems Officer. “The quality of the 30 cm-class imagery that we’re collecting is phenomenal. With the addition of the six state-of-the-art WorldView Legion satellites to our constellation, Maxar can now collect up to 3.6 million sq km of very high-resolution 30 cm-class imagery per day and revisit some locations on Earth up to 15 times per day—capabilities that no other commercial operator can match.”
It’s not just their capabilities that makes Raytheon’s new instruments so remarkable, however. It’s the process Raytheon used to develop them, which utilized cutting-edge digital engineering practices to produce sensors that are not only smaller, lighter, and more capable, but also highly scalable and extremely adaptable.
“Our goal wasn’t just to make one telescope for one customer. It was to develop a broad range of solutions,” Carrigan continued. “We’ve demonstrated that these technologies work on orbit. Now we’re asking ourselves: Where else can we help the warfighter or the community at large move forward? Using the same technologies, we can leverage the SWAP advantage to great effect in many other domains.”
What is digital engineering?
Traditionally digital engineering has focused on tools and technology – the use of computer models and data analysis for product design, development, and delivery – but at Raytheon the process begins with people instead of machines.
“At Raytheon, we have a long history of applying new technologies in such a way that we capture the customer’s need and deliver a better system. That starts with our leadership team,” Carrigan said. “We have leadership that embraces change and says: Things have been done the same way in this industry for 20 or 30 years. What elements of that are a little long in the tooth? What things can we streamline? What technologies and technological assumptions aren’t as valid as they used to be?”
With the support of leaders who challenge the status quo, Raytheon’s engineers can explore with confidence innovative new tools like digital twins—precise 3D models of products and systems that can be manipulated and tested in virtual environments that accurately simulate real-world conditions.
Digital modeling played a key role in the development of WorldView Legion’s imaging payload. Using sophisticated computer analysis, engineers successfully modeled the performance of different materials to determine their physical properties and operational advantages. In doing so, they found an ideal marriage between dissimilar materials. One has a low coefficient of thermal expansion and the other a high stiffness-to-weight ratio, according to Carrigan, whose team combined the materials to create a patented multi-material mirror system that is the beating heart of its next-generation telescope.
“By modeling the behavior of different material types in the same optical system, we arrived at a telescope that has the same effective thermoelastic and imaging properties as legacy systems, but for less cost and less weight,” Carrigan said.
Engineers subsequently used a digital twin of the telescope to foresee how it would integrate with Maxar’s satellite and how it would perform on orbit.
“We also embraced digital automation,” continued Carrigan, whose team created digital work cells that automatically recorded the torques on even the smallest nuts and bolts in its design. “We even went so far as to automate the optical alignment of the telescope by developing a series of actuators and specifically designing the telescope such that it could be aligned by a machine. That automation drove down touch time in the lab, allowing us to operate more hours a day to make the optical alignment and test process more convergent and more predictable.”
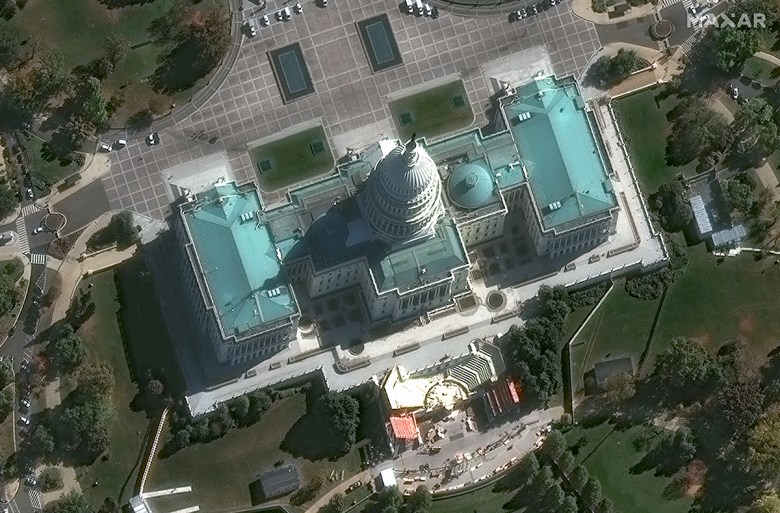
Superior speed and quality
The benefits of digital engineering are as numerous as they are significant. One of the most consequential, for example, is speed.
“Being able to model the complete performance of your sensor—inclusive of inputs from the spacecraft and the electronics—is a game-changer in terms of speed of development,” Carrigan said. “For WorldView Legion, we got to our critical design review within 12 months, which means we had a very successful design process. Programs traditionally take far longer to get to that milestone.”
The same digital models that speed up design streamline manufacturing. “Having a really detailed model of our system allowed us to use model-based work instructions instead of flat-paperwork instructions,” Carrigan continued. “With model-based work instructions, somebody on the floor who’s trying to figure out how to put something together doesn’t have to read the instructions or talk to an engineer. Instead, they can click on the model and look at it in three dimensions to recognize, ‘OK. That’s where that goes.’”
Digital workflows also support quality and mission assurance. Because they can be updated in real time, models are iterative in nature, allowing engineers to continually refine designs and instructions with the learning that takes place during testing and production.
Being able to audit designs and fabrication processes prior to assembly and implementation “leads to a higher-quality product straight out of the gate,” noted Carrigan, who said operators using digital workflows can record quality and mission assurance items in real time using an incorruptible system. “Having a system that will prompt you and help you to record key manufacturing details is a more robust quality management system than what we’ve seen in the past, which translates to affordability by allowing you to catch mistakes early in the process and mitigate them.”
Scaling for success
Looking forward, perhaps the most important benefit of digital engineering will be scalability, suggested Carrigan, who said model-based design and simulation-driven performance testing allow systems to be scaled up or down more efficiently, making it easy to optimize designs for different sizes and performance levels so that the same system can be adapted to multiple use cases.
That’s the case for the new imaging systems, whose underlying design and manufacturing process can easily be scaled to produce versions that have an aperture size of anywhere from 40 centimeters to 150 centimeters for operation in any orbit. “The SWaP advantages of the design are even more important in the GEO and cislunar domains, where everything requires more energy to move,” said Carrigan. This enables new, proliferated mission applications, such as space domain awareness and non-Earth imaging.
Thanks to another benefit of digital engineering—modularity, whereby engineers can easily swap out the imaging sub-systems without redesigning the entire telescope — the all-reflective multi-spectral visible and near-infrared sensor currently flying can be easily modified for missions requiring other spectral bands, such as hyperspectral and mid through long wave infrared (IR).
“Our newest payloads were specifically designed to have a modular, interchangeable backend so you can put different mission modules behind the front-end telescope,” Carrigan said.
Therein lies the promise of digital engineering for remote sensing payloads: It’s not about SWAP-advantaged speed, efficiency, and affordability alone. For applications in defense and commercial industry alike, it’s about using them to scale and adapt on a dime so as to see clearly from space what’s increasingly unseeable on the ground.